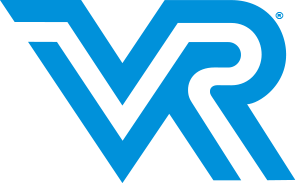
VR® Product Analysis & Information
PolyCo rigorously tests our products for many physical and chemical parameters. We invite you to get a better understanding of why our VR® products are the best barrier products in the industry.
Physical Properties
Independent physical performance tests prove that VR® is superior to vinyl. The chart below compares a 6 mil VR® material to a heavier 8 mil vinyl material, demonstrating conclusively that VR® material outperforms vinyl in all categories.
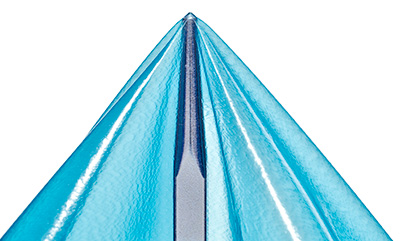
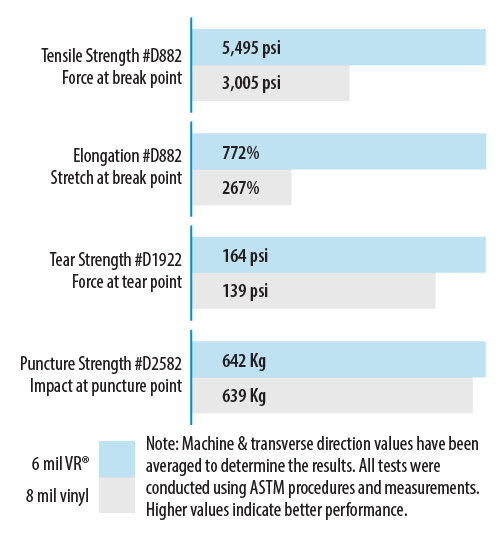
Biological Contaminant Resistance
Personal protective clothing made from VR® film material offers a natural non-stiffening resistance to animal fat and fat-containing fluids. VR® has a unique lustrous finish that is easy to clean for reuse. Fats, oils and other biological contaminants can be easily removed by wiping with a damp cloth, or by washing or rinsing at water temperatures no higher than 180˚F. A liquid washing detergent is most effective as a degreasing and cleaning agent. Regular sanitizing procedures using standard chlorine bleaching agents are recommended for cleaning and decontaminating VR® products. After cleaning, VR® products can be hung to drip dry in ambient temperatures or put into a machine dryer that has an air (cool) cycle–heat cycles should not be used and are not recommended.
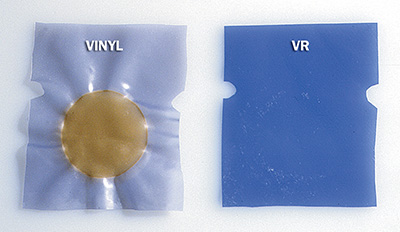
Chemical test with sulphuric acid on vinyl and VR®.
Chemical Contaminants
In comparative independent lab tests, VR® has been proven to be equal or superior to PVC (vinyl) and other alternative materials in chemical resistance–confirming exceptional chemical resistance of VR® to industrial concentrations of hydrofluoric, hydrochloric, sulfuric, and nitric acids under ambient conditions. The lab tests demonstrated that VR® Protective Wear provides excellent protection against accidental exposure or direct contact with hazardous chemicals. Tests were conducted with VR® and vinyl over a 24-hour period. VR® material tested in 4 to 12 mil thickness did not suffer any catastrophic failure (liquid penetration). Vinyl protective wear tested at the same time suffered catastrophic failure when exposed to sulfuric acid. Under the current ANSI (American National Standards Institute) Standard for governing performance requirements for protective clothing, VR® Protective Wear is classified as Partial Body Chemical Protective Clothing. The ANSI prescribed tests are for much shorter periods of exposure than the tests conducted by the independent laboratory performing the tests of VR® Protective Wear. VR® and vinyl were also tested for relative resistance to vapor transmission. VR® was superior to vinyl in vapor transmission resistance. In exposure to sulfuric acid, VR® revealed no evidence of vapor transmission over a 24-hour observation period while vinyl had a catastrophic failure in less than 17 hours. Contact PolyCo for more information about specific chemical contamination resistance.
Climate Controlled Work Environment
VR® film material is especially adapted to cold temperature controlled work environments. VR® material remains soft and supple even at temperatures well below freezing. VR® does not degrade, cold-crack, or become brittle from low temperature use or from exposure to fat, oils, and fat-containing fluids.
Wear Life
The wearing life and reusability of a personal protective garment is essential to many applications. End users nationwide have documented that VR® is more durable than vinyl and many other traditional materials. As the Apron Wear Life Comparison Chart (at the right) illustrates, a cost savings of over 65% a day can be achieved by replacing vinyl with VR®. In this study, VR® and vinyl aprons are assumed to be equal in cost with the wear life of vinyl limited to five days and the wear life of VR® lasting up to 15 days. The cost of vinyl and VR® remains level at 28¢ a day through the first five days with the cost of VR® declining significantly to 9.4¢ a day.
Softness & Weight
In comparative independent lab tests, VR® has been proven to be softer than vinyl (see chart at right). By weight comparison of both VR® and vinyl, the same quantity of both materials show VR® to be 30% lighter than vinyl. A softer feel and lighter weight make VR® a more comfortable product to wear for long periods of time over vinyl.
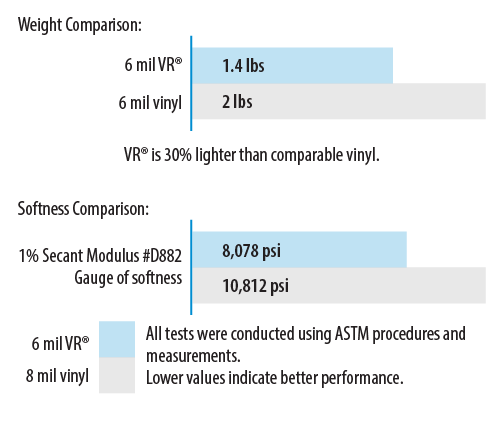
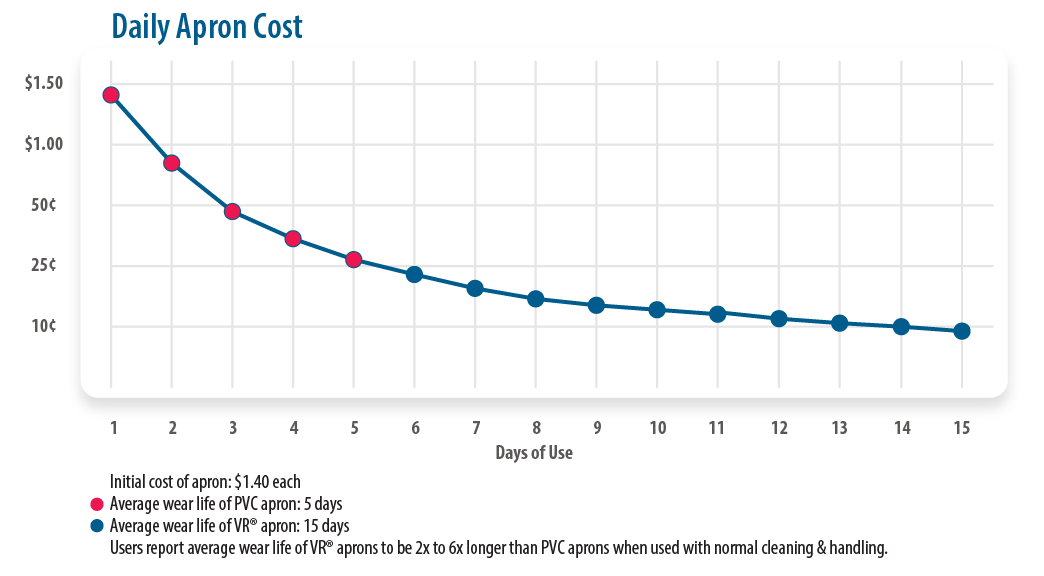
Disposal Cost
In analyzing the cost benefits of replacing vinyl with VR®, attention must be given to the cost-avoidance or waste collection savings achieved from the VR® extended wear life. VR® is lighter weight (up to 50% less than comparable vinyl) provides additional savings in annual waste disposal costs. For example: A plant has 500 employees each wearing one grommeted 8 mil 45” vinyl apron per week for a total usage of 25,000 vinyl aprons. The plant replaces these vinyl aprons with grommeted 6 mil 45” VR® aprons and as a result now uses only 8,333 VR® aprons annually. With the VR® replacement, the plant’s total annual apron disposal cost has been greatly reduced.
Recycling Cost Benefit
VR® is derived from polyolefin plastomer resins that incorporate a new metallocene catalyst technology. Exhibiting very attractive recycling properties, VR® can be blended by most poly film extrusion companies. VR® waste material that is clean and unadulterated (no foreign materials present) commands a premium price from recyclers and film re-processors. The strong bonding and reprocessing qualities of VR® make for excellent recyclability. For example, using the previous illustration, a plant replacing 25,000 vinyl aprons a year with 8,333 VR® aprons can recapture approximately $325.00 (at 15¢/lb.) of the VR® apron cost through a recycling program. Note: These are estimated gross recycling revenues that would contribute to a plant-wide recycling program. Contact PolyCo for more information and guidance in developing a recycling program.
Comfort and Protection
The wearing of VR® personal protective clothing enhances compliance with emerging OSHA ergonomic standards and guidelines. The softness and lighter weigh of VR® contributes to better wearing comfort for the employee during the course of a long work day. Better comfort means that employees will be more attentive to quality and productivity, translating into an economic gain for employers. VR® is odorless and non-toxic. Unlike traditional vinyl, which contains carcinogenic plasticizers that can migrate resulting in material brittleness and surface degradation, VR® is chemically inert and remains stable under conditions of reuse. The innovative design and variety of VR® personal protective wear provides customers with a broad choice of coverage and protection. For optimum comfort, protection and value, VR® is available in many variations of protection as shown in this catalog.
Environmental Safety
PolyCo certifies that VR® personal protective clothing film is approved for direct food contact according to the FDA’s Code of Federal Regulations (21CFR175.300) and is formulated in compliance with the appropriate food additive regulations and guidelines of the USDA for use in direct, prolonged contact with food, meat or poultry products. VR® contains no toxic substances or plasticizers and can be safely land-filled or incinerated with no harm to the environment. If incinerated, VR® product waste emits only nontoxic carbon dioxide and water. Field test comparisons conducted by end users have proven conclusively that VR® Protective Wear is more user friendly–employees enjoy the lighter weight and brilliance of VR® colors. End users have also discovered that VR® is easier to clean and actually gets softer while retaining its strength after repeated uses. UDSA’s HACCP rule includes hygiene requirements related to personal protection apparel. “Reusable disposable items with obvious wear will have to be changed more often.” Under OSHA standard 1910.132, personal protective equipment should be used when hazards to processes or environment, chemical hazards, radiological hazards, or mechanical irritants are encountered in a manner capable of causing injury or impairment to employees through absorption, inhalation, or physical contact. Under these standards, employers are required to analyze their work practices to determine if hazards are present, or are likely to be present, that will necessitate the use of personal protective equipment. Under 1910.132, OSHA also mandates that defective or damaged PPE shall not be used. Reuse of personal protective clothing that becomes brittle and suffers surface alteration after several washes and rinses could potentially violate this OSHA mandate.
VR® Markets
VR® has proven to be a superior replacement for traditional protective apparel used in industries where biological, chemical, and other contaminants pose a significant danger to employees and manufactured products.
Food Processing
VR® Aprons, Sleeves and Gowns have become increasingly popular as cost-effective replacements for traditional vinyl protective apparel in the Food Processing Industry:
- Red Meat & Poultry
- Fisheries & Seafood
- Sausage Makers
- Dairy Operations
- Produce “Further Processors”
- Confectioners
- Beverage Producers
Historically, vinyl aprons, sleeves, and coat aprons (gowns) used for employee protection have demonstrated limited wear life due to the erosion of the vinyl’s plasticizers (softening agents). This erosion is caused by one or more of the following reasons:
a) Frequent Use where the vinyl garment is continually exposed to animal fats and oils
b) Repeated Cleaning or Washing; and
c) Tearing and Cracking from cold work environments.
Since VR® Protective Wear Aprons, Sleeves, and Gowns do not contain plasticizers, their wear life is 3-10 times that of vinyl. This is important to the Food Processing Industry where frequent use and repeated cleaning of protective wear is usual and customary. Another advantage of VR® in the Food Processing Industry is VR®’s lighter weight and softness. Since laboratory studies of VR®’s physical properties have revealed the superiority of VR® to vinyl in strength and durability, VR®’s popularity as a vinyl replacement has continued to grow (4 mil VR® is equal to 6 mil vinyl and 6 mil VR® is equal to 8 mil vinyl). The lighter weight is more comfortable and is less noticeable to the employee during a long workday.
Critical & Controlled Environments
VR® Die-Cut Aprons, Gowns, Sleeves, Boots and Sleeve Gloves are especially adaptable to the protective requirements of critical environments:
- Semiconductor Chip Manufacturing
- Pharmaceutical Laboratories and Manufacturing
- Aerospace Cleanrooms
- Food/Biotech Cleanroom Environments
- Nuclear Waste Disposal
In Particle and Electrostatic Discharge Controlled Environments where chemical resistance of impervious garments is essential, VR® has proven to be superior to traditional vinyl garments. For example, semiconductor cleanrooms work with acid chemicals that pose a significant danger to employees not properly protected with quality, chemical-resistant protective wear. Because of it’s exceptional chemical resistance, low particle count, and surface resistivity, VR® protective apparel is rapidly becoming the product of choice in the semiconductor industry. Contact PolyCo for specific data regarding particle and resistivity levels of typical cleanroom packaged VR® Protective Wear. In critical environments where low-temperature climate control is important, VR® excels with its cold crack resistance. Unlike vinyl, VR®’s softness and durability is not compromised by low temperature work environments and continues to provide comfortable protective wear even in the coldest operating temperatures. With VR®’s low attraction to radioactive particles, Nuclear Power Plant facilities favor the use of VR® Boots and Gowns over vinyl protective wear in the handling and management of radioactive contaminated materials.
Healthcare
VR® is specified as a durable barrier requirement in Critical Environments where there is the potential for biological contamination from bloodborne pathogens. VR® Protective Gowns, Sleeve Gloves, Aprons, Boots, and Sleeves are used in Hospital Sterile Processing, Central Services, Clinical Laboratories, Outpatient, Surgical and other hospital critical care departments.
Manufacturing
Because of the exceptional physical and design attributes of VR® Protective Wear, product manufacturers seeking improved personal protection for their employees from chemical exposure and other toxic and nontoxic contaminants are pleased with the cost-effective performance of VR® compared to other personal protective garments. The ease of cleaning, strength, durability, lightweight comfort, and low price of VR® Protective Wear are attributes that manufacturers and processors prefer or require when specifying employee personal protection. From Automotive to Waste Processing, industries throughout the world are recognizing that VR® Protective Wear is in a class by itself.
VR® Custom Products
VR® is a proprietary material of PolyConversions, Inc., and is being developed into many products formerly dominated by PVC (vinyl) and other materials.
The Many Advantages of VR®
- Puncture Resistance
- Tear Resistance
- Tensile Strength
- Elongation
- Natural Softness
- Recyclability
All make for a replacement material of choice in an age where environmental and ergonomic concerns, combined with long-lasting cost-effectiveness are paramount in new product design.